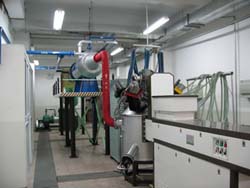
A lab system in simulation of the treatment of medical waste materials through plasma pyrolysis was recently built up by a research team at the CAS Institute of Mechanics in Beijing.
As a pilot facility of the technology with the maximal capacity up to 5 tons per day, the system is composed of a feedstock subsystem, a plasma-burner as the core equipment and a subsystem for post-treatment of the exhaust gas.
The burner subsystem is composed of a furnace, power supplying unit, measurement controls and working gas supply. The post-treatment of exhaust gas includes a gas-quenching device, air-preheating unit, carbon-fiber absorbent unit, exhaust gas burner, ventilator etc. In addition, the system contains cooling pipes, heat diffuser and other accessories.
Via the arc-discharge, the technology is able to raise pyrolysis temperature as high as 1500ºC to 2000ºC, leading to the effective cracking of the chemical bonds of organic materials. Such an approach can wipe out some harmful gases such as NOx, CO and dioxin produced by the combustion with almost zero-emission. Experiments show that this approach only produce a slight amount of pyrolysis gases, carbon black and glass, which are easy for further treatment.
In recent years, the research team has assumed key R&D projects supported in the National Hi-tech Development Program (the so-called "863 Program") and the CAS-hosted Program for Knowledge Innovation on the basis of its research achievements on arc-heading treatment of plastics, rubber, chemical reagents, medical waste and electronic circuit boards. As a result, it has succeeded in buiding up the first system of its kind throughout the country in the compound of Sichuan Province's Chenguang Chemical Research College.
The team is to carry out a cooperative project with a Shenzhen-based firm for an all-round promotion of its own technology in this aspect as a means for transforming its research result into productive forces.